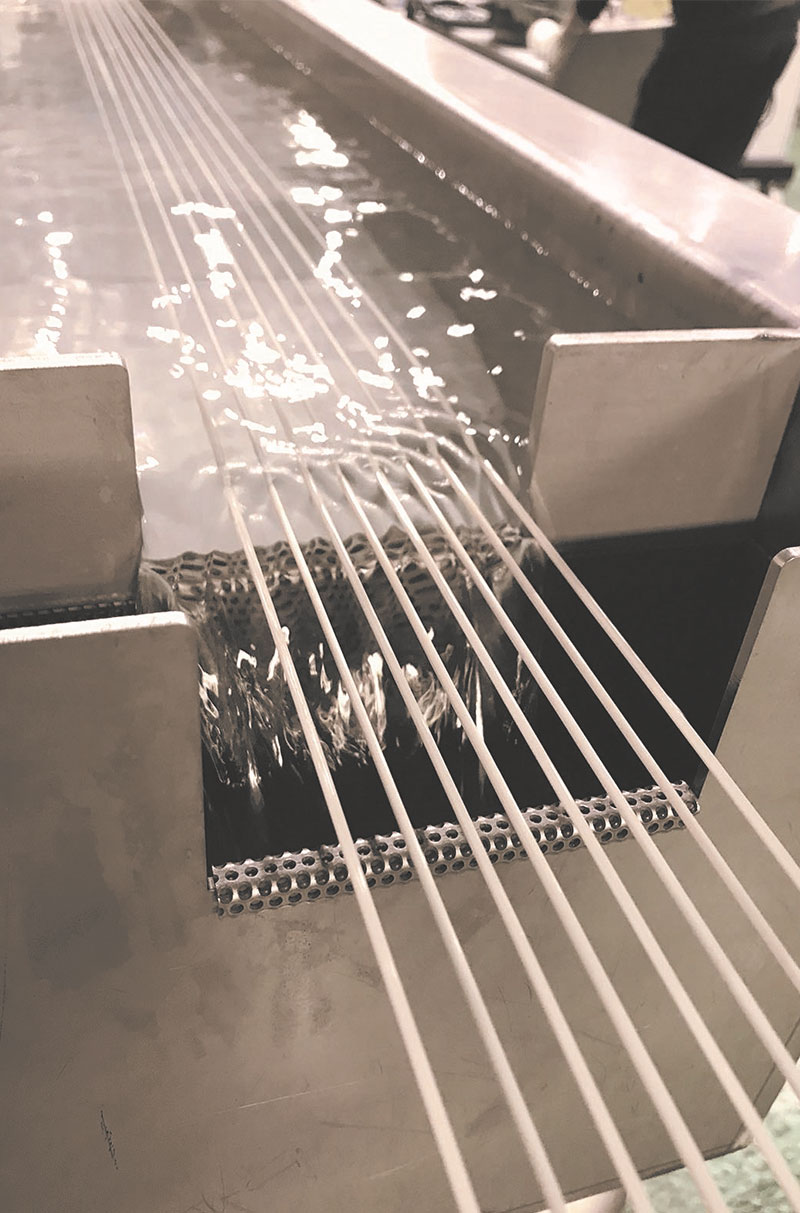
The ips LFT HP pultrusion system stands for the efficient production of long-fibre reinforced thermoplastics.
Intelligent system concept for the production of LFT pellets
Niedernberg, 31.03.2020. Starting immediately, ips Intelligent Pelletizing Solutions GmbH & Co. KG is also supplying systems for the production of long-fibre reinforced thermoplastics (LFT). For this, ips is delivering complete systems from a single source – from planning through construction to commissioning – just as for strand and underwater pelletizing systems.
The ips system LFT HP produces high-quality long-fibre reinforced thermoplastics (LFT) using the pultrusion or strand pulling method. Compared with short-fibre reinforced plastics, components made of long-fibre reinforced thermoplastics have a much greater impact/notched bar impact strength, significantly higher material strength and outstanding rigidity with less material used.
They offer a wide range of processing and design possibilities for the lightweight engineering of materials and structures in particular. “Applications for which metals have mainly been used before can now be realised at lower cost and with less impact on resources by long-fibre reinforced thermoplastics,” explains Simon Weis, Managing Director and responsible for the LFT project at ips. This is particularly true for heavy-duty structural components in the automotive sector, in aerospace and electronics, as well as in plant construction or sports equipment.
Flexible technology
The ips LFT-system is suitable for the production of a wide range of materials with different fibre reinforcement, defined pellet length and different polymers. LFT pellets with fibre contents of between 30 and 60 wt% and throughputs of up to 1,000 kg/h can thus be produced using the system. All common technical polymers can be used as melts, while glass, carbon and aramid fibres as well as hybrid combinations come into consideration as reinforcing fibres. The cut length of the strands can vary between 6 – 25 mm. The fibre lengths contained correspond exactly to the cut length of the pellets.
“Our objective was to develop a more efficient manufacturing technology for long-fibre reinforced polymer pellets. Our 8-strand pilot system is operating successfully. It is also available for customer trials. We can use it to check on individual customer requirements quickly and product small quantities for test purposes,” says Simon Weis.
The components
Starting point for the system is the tangential, controlled unwinding of the rovings to avoid twists. The required polymer melt is supplied via a powerful extruder. The impregnating tool and the post-forming modules are at the heart of the LFT-system. Here, the spread rovings are impregnated with polymer melt. The straightforward design of the impregnating tool impresses through flexible setting of the fibre tension depending on fibre type, fibre titre and process speed. This guarantees an optimum degree of impregnation of the fibre filaments.
The impregnating process is supported by a post-forming nozzle and shaping rollers. In this phase of the system, LFT strands are calibrated for their target fibre content and then cooled. The forming roller or forming roller module post-forms the strands as well as smoothing and cooling them. Depending on the polymer type the LFT strands must be cooled by water. There is a strand cooling trough with integrated process water system available as an option for this purpose.
Roller or belt draw-off ensure constant draw-off speed and the even gathering of all strands. The strands are cut to the required pellet length with the aid of the strand pelletizer.
Simple operation
All modules of the ips LFT-system are controlled via a central user interface. This covers everything from draw-off speed through extruder throughput to cut length of the pellets. All components have variable control.
The development of the ips system for the production of LFT pellets is a joint project between ips and Cetex Institut gGmbH, Institut für Textil- und Verarbeitungsmaschinen (Institute for Textile and Processing Machines) at the Technical University of Chemnitz – promoted by the Zentrale Innovationsprogramm Mittelstand ZIM (Central Innovation Program for Medium-Sized Businesses ZIM).